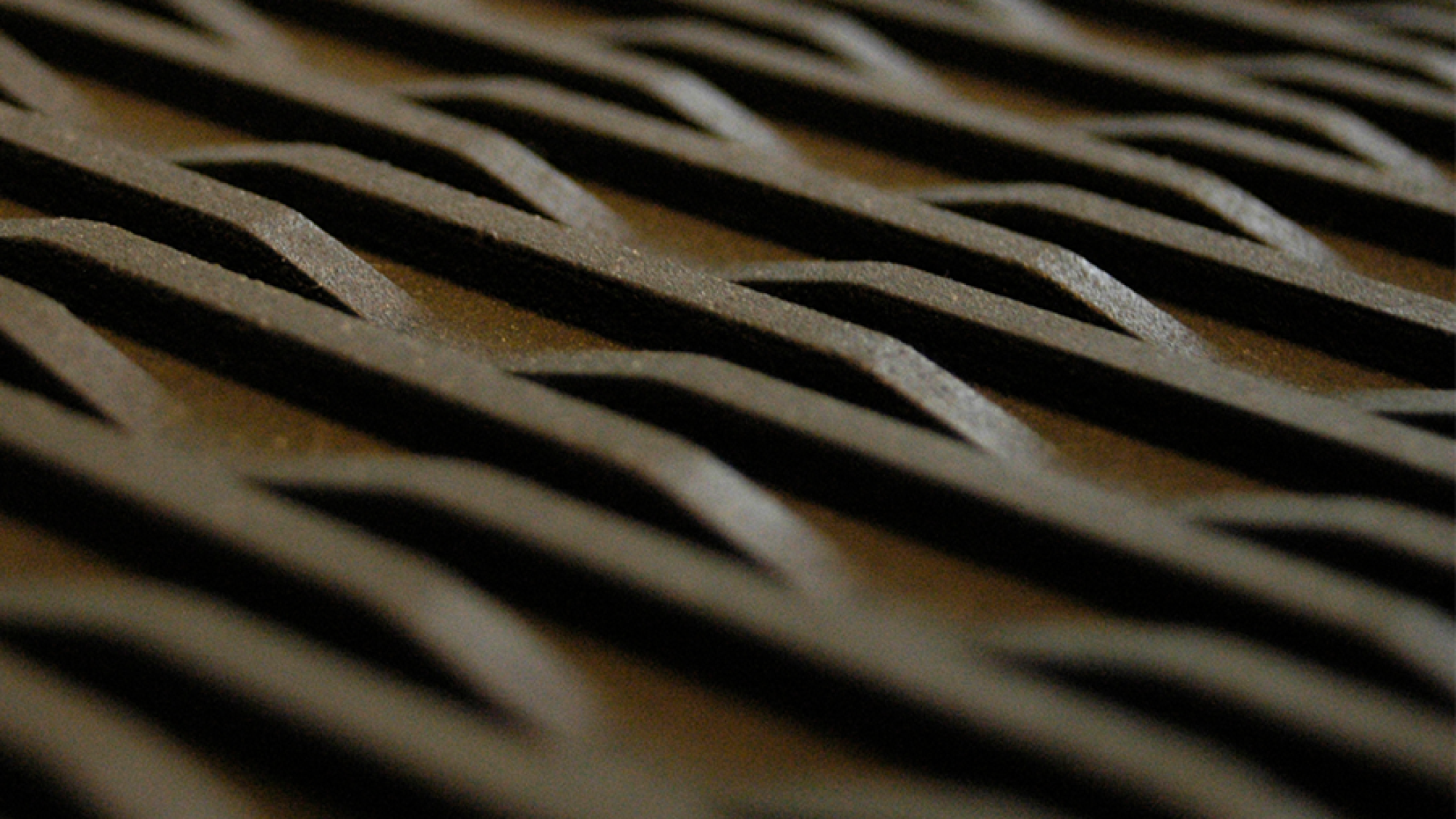
Kompressionsgjutning av gummi
Processen för kompressionsgjutning av gummi inleds med tillverkandet av ett gjutverktyg, vanligtvis tillverkad av metall, med formrum/kaviteter som representerar den önskade form och storlek som gummiprodukten ska ha. Formen är består oftast av två formskapande verktygshalvor, en övre och en undre verktygshalva, som kan öppnas och stängas i förhållande till varandra.
För att påbörja processen för kompressionsgjutning förbereds en noggrant avvägd mängd blandat gummi i varierande former (ämnen) beroende kaviteternas utformning. Ämnena som placeras i kaviteterna tillverkas genom ett skärningsförfarande direkt från gummiblandningsplattor eller så extruderas gummiblandningen genom ett munstycke som formar en profil som kapas i lämpliga längder.
Dessa ämnen placeras sedan i kaviteterna och formverktyget stängs försiktigt för att säkerställa att gummiblandningen fördelas jämnt i kaviteterna. Detta är viktigt för att kunna uppnå gummiproduktens önskade egenskaper och dimensioner.
Efter att gummit placerats i kaviteterna och formverktyget stängts inleds vulkaniseringsprocessen med hjälp av tillförande av värme och tryck. Värmeöverföringen mellan formverktyg och gummi är avgörande för att vulkaniseringsprocessen ska starta. Då gummits värmeledningsförmåga är låg värms gummit upp långsamt och vulktiden är därför relativt lång.
Typiska vulktider är från minuter för tunt gods till timmar för tjockväggiga produkter. I det senare fallet är det effektivt att förvärma gummit i exempelvis en värmeugn eller genom extrudering av gummiblandningen.
Vulkanisering av gummi är en kemisk process där rågummi omvandlas till en starkare och mer elastisk form genom att korsbinda polymerkedjor. Denna process ger gummit dess slutliga egenskaper så som slitstyrka, elasticitet och kemikalieresistens.
Efter en förutbestämd vulkstid öppnas formverktyget och den färdiga gummiprodukten avlägsnas ur formverktyget. Eventuella materialöverskott avlägsnas bort för att ge produkten dess slutliga form och yta. För att säkerställa att kaviteterna i verktygs fylls krävs en viss "överladdning" av material, ofta i storleksordningen 5 - 10%.
Fördelarna med kompressionsgjutning är främst följande:
1. Metoden är enkel med relativt billiga verktyg. Lämplig vid små serier.
2. Möjliggör formgjutning av flera olika komponenter och material.
3. Lämpar sig för produkter med stor yta eller stor utbredning.
4. Kan användas för gummiblandningar med hög viskositet och dålig flytförmåga.
5. Kompressionsgjutning är ett bra alternativ när man efterfrågar produkter med komplext geometrier och varierande godstjocklek.
Sammanfattningsvis är kompressionsgjutning av gummi en beprövad, pålitlig och flexibel tillverkningsmetod som har använts under många år. Dess förmåga att producera komplexa detaljer med hög precision, kombinerat med kostnadseffektivitet vid små till medelstora produktionsserier gör det till ett alternativ som ofta anvnds ingom gummindustrin.
På HGF har vi ett flertalet kompressionspressar i olika storlekar och med olika låstryck som möjliggöra tillverkning av allt från små till stora gummidetaljer. En av våra styrkor öär att vi har en stor mix av olika kompressionspressar vilket ger oss en stor flexibilitet när vi föreslår verktygsläsning med avseende på antal kaviteter.
För att påbörja processen för kompressionsgjutning förbereds en noggrant avvägd mängd blandat gummi i varierande former (ämnen) beroende kaviteternas utformning. Ämnena som placeras i kaviteterna tillverkas genom ett skärningsförfarande direkt från gummiblandningsplattor eller så extruderas gummiblandningen genom ett munstycke som formar en profil som kapas i lämpliga längder.
Dessa ämnen placeras sedan i kaviteterna och formverktyget stängs försiktigt för att säkerställa att gummiblandningen fördelas jämnt i kaviteterna. Detta är viktigt för att kunna uppnå gummiproduktens önskade egenskaper och dimensioner.
Efter att gummit placerats i kaviteterna och formverktyget stängts inleds vulkaniseringsprocessen med hjälp av tillförande av värme och tryck. Värmeöverföringen mellan formverktyg och gummi är avgörande för att vulkaniseringsprocessen ska starta. Då gummits värmeledningsförmåga är låg värms gummit upp långsamt och vulktiden är därför relativt lång.
Typiska vulktider är från minuter för tunt gods till timmar för tjockväggiga produkter. I det senare fallet är det effektivt att förvärma gummit i exempelvis en värmeugn eller genom extrudering av gummiblandningen.
Vulkanisering av gummi är en kemisk process där rågummi omvandlas till en starkare och mer elastisk form genom att korsbinda polymerkedjor. Denna process ger gummit dess slutliga egenskaper så som slitstyrka, elasticitet och kemikalieresistens.
Efter en förutbestämd vulkstid öppnas formverktyget och den färdiga gummiprodukten avlägsnas ur formverktyget. Eventuella materialöverskott avlägsnas bort för att ge produkten dess slutliga form och yta. För att säkerställa att kaviteterna i verktygs fylls krävs en viss "överladdning" av material, ofta i storleksordningen 5 - 10%.
Fördelarna med kompressionsgjutning är främst följande:
1. Metoden är enkel med relativt billiga verktyg. Lämplig vid små serier.
2. Möjliggör formgjutning av flera olika komponenter och material.
3. Lämpar sig för produkter med stor yta eller stor utbredning.
4. Kan användas för gummiblandningar med hög viskositet och dålig flytförmåga.
5. Kompressionsgjutning är ett bra alternativ när man efterfrågar produkter med komplext geometrier och varierande godstjocklek.
Sammanfattningsvis är kompressionsgjutning av gummi en beprövad, pålitlig och flexibel tillverkningsmetod som har använts under många år. Dess förmåga att producera komplexa detaljer med hög precision, kombinerat med kostnadseffektivitet vid små till medelstora produktionsserier gör det till ett alternativ som ofta anvnds ingom gummindustrin.
På HGF har vi ett flertalet kompressionspressar i olika storlekar och med olika låstryck som möjliggöra tillverkning av allt från små till stora gummidetaljer. En av våra styrkor öär att vi har en stor mix av olika kompressionspressar vilket ger oss en stor flexibilitet när vi föreslår verktygsläsning med avseende på antal kaviteter.